Influencia de la ceniza de cáscara de arroz en los tiempos de fraguado de un concreto f’c=280 kg/cm2
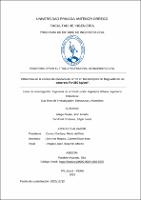
Fecha
2024Autor(es)
Aliaga Zavala, Joan Amado
Sandoval Gonzales, Edgar Josué
Metadatos
Mostrar el registro completo del ítemResumen
La ceniza de cáscara de arroz es un componente que presenta elementos químicos (Óxidos) similares al cemento Portland, convirtiéndolo en un material puzolánico beneficioso para el concreto. Por ello es que buscamos darle un uso a aquello que se le puede catalogar como “desperdicio” y lograr que sea una alternativa más para el mundo de la tecnología del concreto.
En nuestra región La Libertad observamos grandes zonas arroceras, siendo una de ellas el valle Jequetepeque, en donde las grandes empresas seleccionan la materia prima que son los granos de arroz, dejando muchas veces de lado el desperdicio que queda: la cáscara de arroz.
La presente Tesis tiene como principal objetivo conocer la influencia que presenta la ceniza de cáscara de arroz en los tiempos de fraguado del cemento Portland tipo I. Posteriormente, dichos resultados se implementarán en el diseño de un concreto f’c= 280 kg/cm2 para evaluar su influencia en los costos finales. Dicha ceniza será obtenida de las zonas arroceras del valle Jequetepeque, específicamente de la ciudad de Chepén.
En esta investigación se procedió en primer lugar a obtener la caracterización química de la ceniza de cáscara de arroz que se utilizó durante el estudio, para observar cada componente presente en esta puzolana y poder clasificarla según la ASTM C 618-19.
Posteriormente se hizo el ensayo de consistencia normal del cemento, donde determinamos que la fluidez correcta se daba con la relación agua-cemento (a/c) de 0.30. Con este dato obtenido se procedió a realizar el ensayo principal de la presente tesis, que es determinar los tiempos de fraguado.
En base a estudios previos donde se concluyó que el concreto logra su mayor resistencia a la compresión al reemplazar 5% ceniza de cáscara de arroz por cemento, decidimos utilizar los porcentajes de 3%, 4% y 5% para el ensayo de la Aguja de Vicat. Se realizaron un total de 12 muestras, siendo 3 para el diseño de pasta patrón, otras 3 para el diseño que tenía 3% de CCA, 3 para el que contenía 4%, y 3 para el de 5%. Los resultados determinaron que el concreto patrón tenía un fraguado inicial de 186 minutos y un fraguado final de 290 minutos. El diseño con 3% de CCA tuvo como fraguado inicial y final de 183 y 260 minutos, respectivamente. La pasta con 4% de CCA alcanzó un fraguado inicial de 185
vi
minutos y un fraguado final de 275 minutos. Finalmente, el ensayo que presentaba 5% de CCA tuvo 178 minutos y 295 minutos de fraguado inicial y final, respectivamente. Concluyendo así que el diseño que mejor se comporta era el que presentaba 3% de ceniza de cáscara de arroz.
Después de obtener las materias primas para el concreto (los agregados), se procedió a ensayarlos para determinar que cumplan todos los requerimientos y ensayos de la norma. Con los resultados obtenidos se diseñó el concreto f’c= 280 kg/cm2 siguiendo las indicaciones de la ACI 211.
Por último, se determinaron los costos unitarios por m3 tanto para el diseño patrón f’c= 280 kg/cm2 como para los que tenían 3%, 4% y 5% de ceniza de cáscara de arroz, observando que los costos disminuyen para los tres diseños con porcentajes de CCA debido al bajo costo del mencionado elemento puzolánico. El diseño más bajo fue el de 5% costando S/ 525.30, seguido del diseño de 4% con un costo de S/ 526.51, y por último el diseño con 3% de CCA con un valor de S/ 527.73 por m3, en comparación al modelo patrón que tuvo un costo de S/ 531.36 Rice husk ash is a component that has chemical elements (Oxides) similar to Portland cement, making it a beneficial pozzolanic material for concrete. That is why we seek to give a use to what can be classified as “waste” and make it another alternative for the world of concrete technology.
In our La Libertad region we observe large rice growing areas, one of them being the Jequetepeque valley, where large companies select the raw material that is rice grains, often leaving aside the waste that remains: the rice husk.
The main objective of this Thesis is to know the influence of rice husk ash on the setting times of Portland cement type I. Subsequently, these results will be implemented in the design of a concrete f'c= 280 kg/cm2 for evaluate its influence on final costs. Said ash will be obtained from the rice-growing areas of the Jequetepeque valley, specifically from the city of Chepén.
In this research, we first proceeded to obtain the chemical characterization of the rice husk ash that was used during the study, to observe each component present in this pozzolan and be able to classify it according to ASTM C 618-19.
Subsequently, the normal cement consistency test was carried out, where we determined that the correct fluidity occurred with the water-cement ratio (w/c) of 0.30. With this data obtained, the main test of this thesis was carried out, which is to determine the setting times.
Based on previous studies where it was concluded that concrete achieves its highest compressive strength by replacing 5% rice husk ash with cement, we decided to use the percentages of 3%, 4% and 5% for the Needle Test. Vicat. A total of 12 samples were made, 3 for the pattern paste design, another 3 for the design that had 3% RHA, 3 for the one that contained 4%, and 3 for the one with 5%. The results determined that the master concrete had an initial setting of 186 minutes and a final setting of 290 minutes. The design with 3% RHA had an initial and final setting of 183 and 260 minutes, respectively. The paste with 4% RHA reached an initial setting of 185 minutes and a final setting of 275 minutes. Finally, the test that presented 5% RHA had 178 minutes and 295 minutes of initial and final setting, respectively. Thus, concluding that the design that performed best was the one that presented 3% rice husk ash.
After obtaining the raw materials for the concrete (the aggregates), they were tested to determine that they meet all the requirements and tests of the standard.
viii
With the results obtained, the concrete f'c = 280 kg/cm2 was designed following the instructions of ACI 211.
Finally, the unit costs per m3 were determined both for the standard design f'c = 280 kg/cm2 and for those with 3%, 4% and 5% of rice husk ash, observing that the costs decrease for the three designs with RHA percentages due to the low cost of the aforementioned pozzolanic element. The lowest design was the 5% design costing S/ 525.30, followed by the 4% design with a cost of S/ 526.51, and finally the design with 3% RHA with a value of S/ 527.73 per m3, in comparison to the standard model that had a cost of S/ 531.36
Palabras clave
Colecciones
- Ingeniería Civil [1260]